Environmental Remediation
Refurbished System for a Former Gas Station in a Small Town
MAE2 was approached by a consultant that needed a system that could provide multiple technologies to remediate a site with significant free product gasoline.
The site had been partially studied by a previous consultant and there was no additional funding for further study.
It was decided that installing a system that had a large flow, pressure, vacuum and treatment capacity would allow for operational flexibility and cover any unexpected process needs. Using a refurbished system reduced the installation costs and allowed the system to be on-site significantly sooner.
The consultant knew from experience that they could rely on MAE2 for quality workmanship and long term product support and be delivered a high quality, dependable refurbished system.
The consultant selected MAE2 to build a vacuum enhanced groundwater pump and treat and air sparge remediation system that incorporated down well groundwater pumps and high vacuum DPE (Dual Phase Extraction) in order to remove the free product and lower the dissolved phase gasoline concentrations. The system also includes Air Sparging in order to volatilize VOC’s in the vadose zone and stimulate bio activity.
MAE2 recommended a high vacuum 30 HP rotary claw pump along with QED pneumatic auto pumps to dewater the wells and to expose more soil the influence of the SVE and the rotary claw compressor used for air sparging. The rotary claw vacuum pump was chosen to allow the system flexibility to operate at a wide range of vacuum levels.
The flexibility allows the system to operate at low vacuum to help slurp the free product in the wells while pumping at a low rate to maximize the initial free product recovery. The pneumatic auto pumps operate on demand with a 15 HP reciprocating air compressor providing the air supply needed for pumping. The Groundwater Treatment system consists of an air water separator, an oil water separator to remove free product and a removable tray air stripper to remove the dissolved phase gasoline before discharging to surface water.
To start free product removal the consultant operated only the pneumatic downwell pumps. Once the free product is reduced in the recovery wells, the well pumps will be set deeper and pump at a higher volume and the vacuum from the SVE will be increased. The rotary claw sparge compressor will also be started to maximize the treatment and reduce the project run time. An enclosed steel frame utility trailer enclosure allows for maximimum flexibility and mobility.
The regulatory agency requires consistent run time for all approved systems. The system provides run time hours, vacuum trends, and water flow totals recorded through the PLC control panel. The cellular connection allows full system control and data through easy-to-use web browser access. The instant alarm notification and remote control allows the consultant to immediately respond to any changing site conditions and maximize system run time.
This Remediation System uses the following components and subsystems-
Rotary Claw Vacuum Pump
Removable Tray Air Stripper
Progressive Cavity Transfer Pump
Reciprocating Air Compressor
Down well Pneumatic Pumps
Rotary Claw Compressor
Heating Oil Removal System for an Apartment Building
MAE2 worked with a consultant who needed a pump and treat system to extract groundwater from two wells and then re-inject the treated water.
The project goal is to remove heating oil from the groundwater, removing any long-term liability concerns for the apartment complex owners
MAE2 built the system using a custom modified cargo container. The enclosure consisted of two rooms. The first room contained the control panel and the air supply compressor. The second room included the water treatment system and was built to meet the requirements for Class 1 Div 2 hazardous environments. Both rooms included lights, ventilation fans and heat. The system components were completely tested before shipping to make certain the system was ready to run on site with no downtime.
The system is a Pump and Treat and Groundwater Treatment system designed for up to 30 GPM water flow. MAE2 provided 2 QED AP4+ Pneumatic Groundwater Pumps complete with downwell air, water discharge and exhaust hoses and well caps. The system had a Reciprocating Air Compressor connected to an air supply manifold that included pressure and flow controls. Air hose was used to connect the trailer air supply manifold with the downwell pneumatic pumps.
The water discharge from the pumps connected to the multi point extraction manifold. The manifold piped the extracted groundwater to an Oil Water Separator to remove any free product heating oil. Any free fuel that is collected gravity drains into a 250 gallon product holding tank. A centrifugal transfer pump sends the water to two parallel high pressure fiberglass carbon vessels for treatment before discharge. The water passes through a flow totalizer to record total gallons treated prior to discharge to sanitary sewer. The system is controlled by a custom relay control panel that includes an externally mounted flashing alarm light.
Components used in this system
Relay Control panel
Reciprocating Air Compressor
Down well Pneumatic Pumps
Custom Cargo Container Enclosure
Rental System for Remediation of a Redevelopment site.
MAE2 was selected to provide a rental system to remediate a former gas station site that had been redeveloped.
MAE2 had previously provided a rental system that successfully removed most of the gasoline contamination from the site but had to be removed to allow for construction when the property was sold for redevelopment. The remaining fuel contamination was concentrated in a smaller area. Renting a system was a perfect option for this site. After the site was redeveloped, a different smaller system was chosen to complete the site remediation saving both rental and operating cost.
The fuel contamination was limited to the vadose zone soils, so the system selected was an air sparge, soil vapor extraction system. This involves pumping air into the pressure wells to volatilize residual fuel and to stimulate bio remediation activity. The soil vapor extraction creates further volatilization and extraction of soil vapors. The system is enclosed in an 8’ x 14’ utility trailer with insulated walls and ventilation fan and lights.
The air sparge unit is a 7.5 HP Rotary Vane Compressor capable of providing 55 ACFM @ 20 PSI to a two point manifold with each leg including a pressure gauge and a ball valve. The vapor wells are connected to a two point extraction manifold that includes a gate valve and vacuum gauge for each leg. The soil vapor extraction consists of a marine grade aluminum vapor liquid separator and a 15 HP regenerative vacuum blower capable of 350 SCFM @ 85” WC vacuum. The vapor liquid separator includes a centrifugal transfer pump to empty any water that is collected. The system includes a relay based control panel to allow for simple fully automated control.
This Remediation System uses the following components and subsystems
Regenerative Vacuum Pump
Rotary Vane Air Compressor
Rotary Claw Compressor
Pilot Test and Startup Support.
MAE2 was contacted by a consultant that needed equipment and support for a high vacuum pilot test.
The contractor wanted to run a pilot test to try to get influence in an area of the site the was dominated by above ground storage tanks and railroad tracks. The soils at the site were very tight, requiring a unit that could operate at vacuum levels 15″ HG and higher. They contacted MAE2 for the pilot test unit and additional on-site support and training.
MAE2 provided a Multi-Phase Vacuum System with a Liquid Ring Vacuum Pump. The Liquid Ring Pump is the best option for vacuum applications that require vacuum levels exceeding 24″ HG. Liquids removed during the pilot test collected in the Vapor Liquid Separator and then were pumped to an on site frack tank. The system was connected to a mobile generator to provide electrical power.
MAE2 provided an on-site technician to help with the set up of the system and generator and training on system operation. The system was connected to a horizontal well that was located under the train tracks and tank farm. The pilot test went well and it proved that high vacuum extraction created the desired air flow and influence.
The following system components were used in the pilot system.
Liquid Ring Vacuum Pump
Vapor Liquid Separator
Progressive Cavity Transfer Pump
PLC Control Panel
Refurbished Dual Phase Extraction and Groundwater Treatment System with Thermal Oxidizer
MAE2 was approached by a consultant that had performed a Corrective Action Plan and recommended a multi-phase extraction system to perform remediation at a gas station site.
The consultant also required a thermal oxidizer to treat the vapors removed from the site. In order to keep the budget costs low the consultant looked for a high quality, dependable refurbished system, along with a rental oxidizer.
The consultant knew from experience that they could rely on MAE2 for quality workmanship and long-term product support.
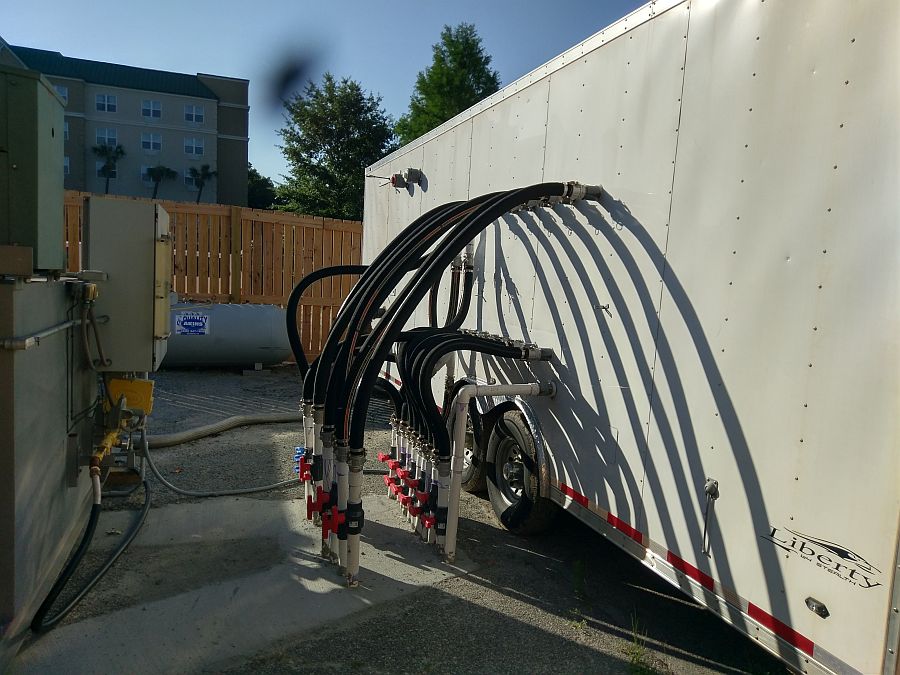
An existing Dual Phase Extraction system refurbished for this project
MAE2 took an existing Dual Phase Extraction system from our fleet and made minor modifications. The control panel was updated with a new touch screen control panel and remote telemetry system. The system components were completely tested, and a full O & M and cleaning was conducted to make the system site ready.
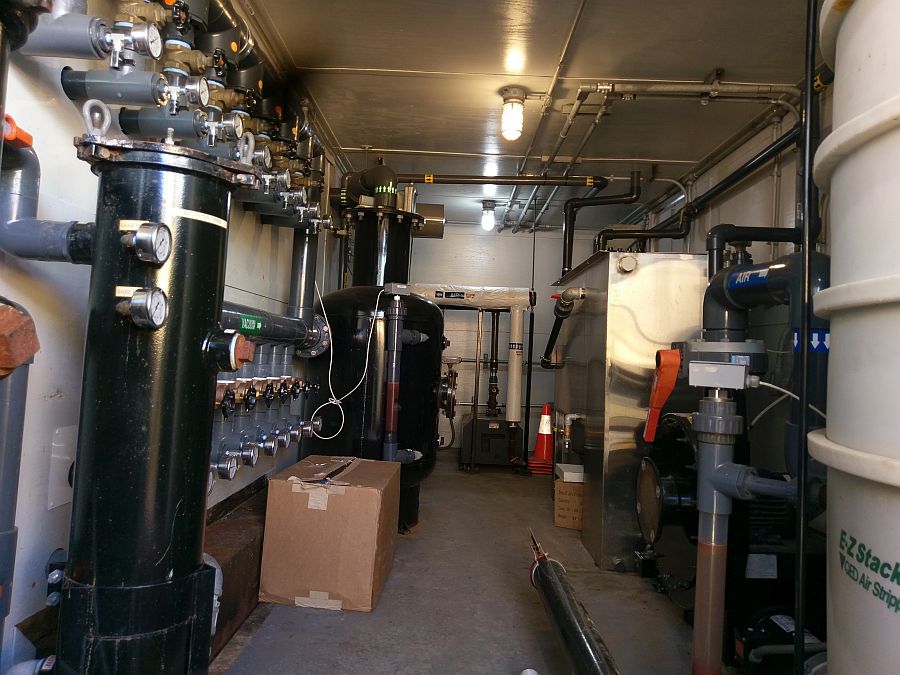
Existing DPE internal view
The system is a Dual Phase Extraction and Groundwater Treatment system designed for 20 GPM water flow and 330 ACFM vapor flow at 25” HG. There is a 12 point extraction manifold that pulls both water and vapor from the extraction wells using two 10 HP rotary claw vacuum pumps mounted in parallel. The extracted groundwater is collected in the 120 G Vapor/Liquid separator and then pumped to an Oil Water Separator (OWS) using a progressive cavity transfer pump.
Any free fuel that is extracted is collected in the OWS and gravity drains into a product holding tank. The water is pumped from the OWS through a bag filter, to remove suspended solids, and then to a Poly Stackable Tray Air Stripper. After the air stripper the water is pumped through two bag filters in series, to remove any remaining suspended solids and two medium pressure steel carbon vessels for final treatment before discharge. The OWS pump and Air Stripper pump are centrifugal transfer pumps. The system is controlled by a custom PLC control panel that allows for remote access and control using web based telemetry.
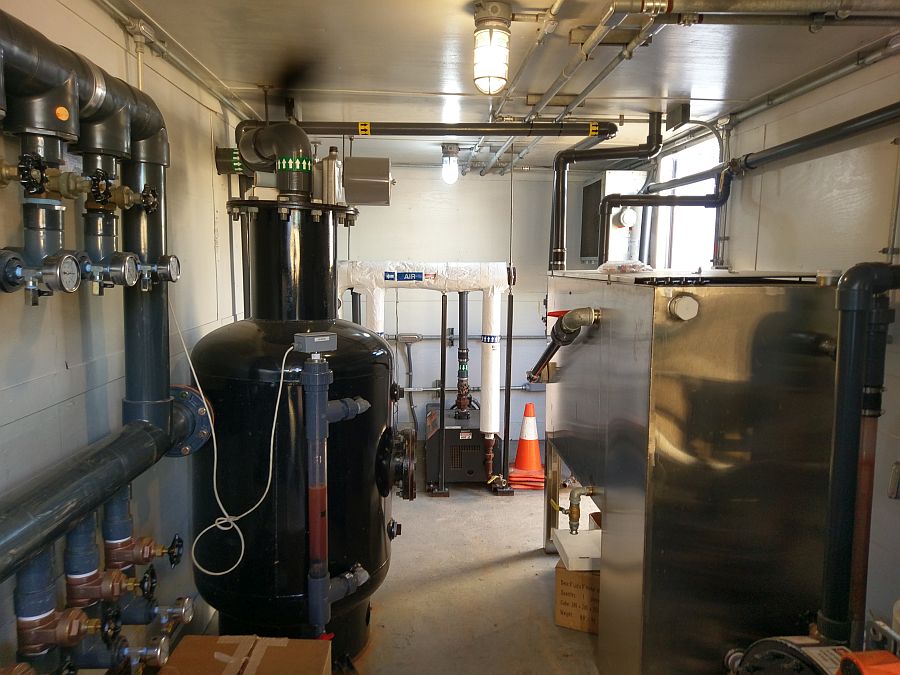
Dual Phase Extraction system components
The vapors pulled from the ground contain higher concentrations of hydrocarbon than allowed without treatment. MAE2 provided a rental Gas Fired Thermal Oxidizer to destroy 99+% of the hydrocarbons. The oxidizer uses the hydrocarbons pulled from the ground to fuel the thermal oxidizer, efficiently destroying them.
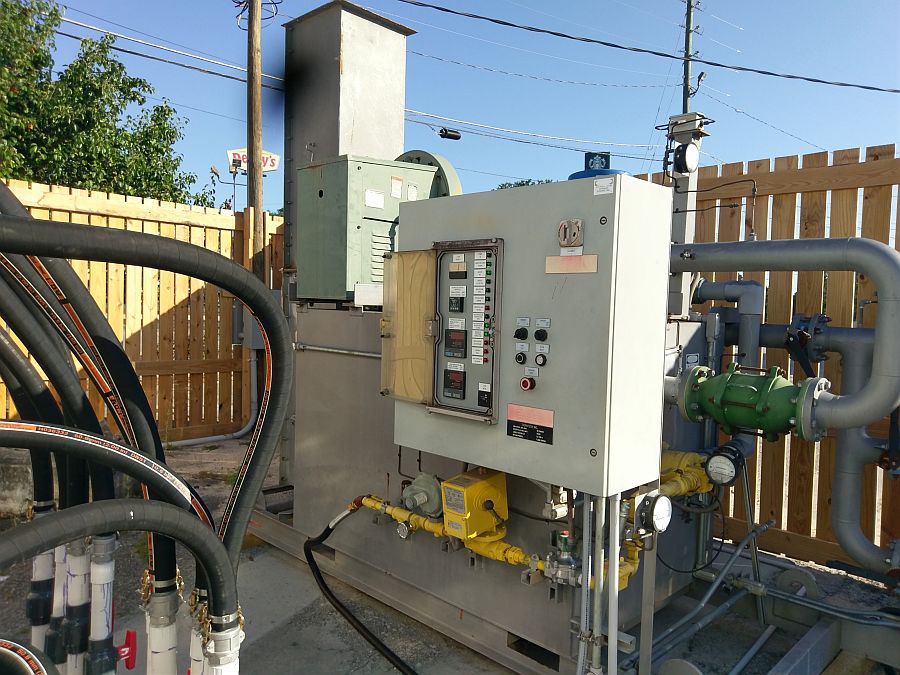
External Thermal Oxidizer
Components used in this system
Environmental Remediation System Finds New life at a New Site.
Reuse of an Existing Remediation System results in significant savings and reduced training time.
Many consulting firms have possession of existing remediation systems that have been used to complete the remediation at a site and achieve site closure. Reusing that system on a new site can save cost and increase the bottom line for the consulting firm. Additionally, the field operators are already familiar with the system maintenance and operation. MAE2 has helped many consultants update and refurbish existing systems to help them maximize their resources and provide more competitive solutions to their clients
MAE2 was recently contracted by a consultant to refurbish a used system from their inventory to prepare it and customize it for use at a new site. The refurbished system allowed the consultant to use a system they were familiar with while keeping the budget within approved funding levels.
The system was transported to our manufacturing facility. The MAE2 technical staff thoroughly tested the system and inspected each component. All required maintenance was performed and any components and parts that were beyond their useful life, due to wear and tear, were replaced or upgraded.
The system and controls were customized to meet the requirements of the new site. The end result was a customized, reliable system at a considerable savings when compared to a brand new system. Additionally the consultant’s field staff was already familiar with the system, which greatly reduced labor and training time and costs.
The system is a Dual Phase Extraction and Groundwater Treatment system designed for 10 GPM water flow and 500 ACFM vapor flow at 25” HG. There is a 5 point extraction manifold that pulls both water and vapor from the extraction wells using two 10 HP rotary claw vacuum pumps in parallel. The extracted groundwater is collected in the 120 G Vapor/Liquid separator and then pumped to an Oil Water Separator using a progressive cavity transfer pump. Any free fuel that is extracted is collected in the OWS gravity drains into a product holding tank.
The water is pumped using a centrifugal transfer pump into the Poly Stack-able Tray Air Stripper. The Pressure Blower forces air through the air stripper trays removing over 99% of the dissolved fuel from the water. The water is then pumped through two bag filters in parallel and one high pressure steel carbon vessels for final polishing treatment before discharge. The Air Stripper uses another centrifugal transfer pump to pump the water through the bag filters, carbon and to the final discharge point. The system is controlled by a newly upgraded custom PLC control panel that allows for remote access and control using web-based telemetry.
Components used in this system
Progressive Cavity Transfer Pump
Poly Stack-able Tray Air Stripper
Pressure Blower
Neighborhood Home Heating Oil Bio Vent Remediation System in NJ Suburb
MAE2 was selected to design and build a remediation system for a backyard home heating oil site in an established residential neighborhood after providing the most responsive and cost effective bid.
The consultant approached MAE2 with a unique and challenging project. A home heating oil tank had leaked, and after removing most of the contaminated soil the consultant recommended a Bio Vent system to remediate the remaining contamination under the homeowner’s property and the neighboring house. There were several challenges that needed to be overcome with the system design. The power supply in the neighborhood was limited to single phase power. The small lot sizes and the quiet neighborhood setting required the system to operate quietly to avoid disturbing the neighbors.
The system needed to have a small footprint to fit in the backyard. Finally the insurance company claim required that the system construction could not exceed a fixed budget.
MAE2 responded to the RFP by proposing a Regenerative Vacuum Pump, in a Custom Sound Enclosure. The Regenerative Vacuum Pump was chosen because it provides the vacuum and flow required and operates at a lower decibel level than other possible pump choices.
The consultant designed the site so that there were two parallel trenches. The Bio Vent system included a custom manifold so that the system could pull a vacuum from one trench and simultaneously draw fresh air into the opposite trench through the custom manifold. The trenches were placed close enough to one another that each trench was within the radius of influence of the other trench. This allowed the vacuum influence to introduce fresh air to the subsurface and provide oxygen to support the bio degradation of the fuel contamination.
A Custom Sound Enclosure was built to keep the sound of the blower from disturbing the neighboring homes. The system has removable side panels to provide easy access to the equipment and insulated sound hoods and sound insulation inside the walls. The sound enclosure completely mitigated the equipment operating noise.
The system required was built using a relay based control panel including a Variable Frequency Drive (VFD). The VFD was added to the control panel because single phase power was the only power supply available. In order for the system to achieve the performance required for vacuum and air flow needed to be successful it required a three phase vacuum pump. The VFD converts the single phase power to three phase power and also offers additional motor protection and motor speed control. Adjusting motor speed provides electrical power savings and also a reduction in operating noise.
The system provides run time hours, amperage levels, and local alarm lights and alarm reset. The system also includes an adjustable operating timer that allows custom user setting so the system can be programmed to automatically run during daytime hours and shut down during nighttime hours.
MAE2 personnel met the consultant onsite to provide system testing, commissioning and operational training.
This Bio Vent Remediation System uses the following components and subsystems
Regenerative Vacuum Blower
Custom Sound Enclosure
Short Term Rental System for a Groundwater Re-circulation Event at a City Gas Station
MAE2 installed a flexible pump and treat system for groundwater remediation, from our fleet of available rental systems.
MAE2 worked with a consultant who needed a pump and treat system to extract groundwater from two wells and then re-inject the treated water. The project scope called for a 1-week site event and a flexible, and readily available system was required.
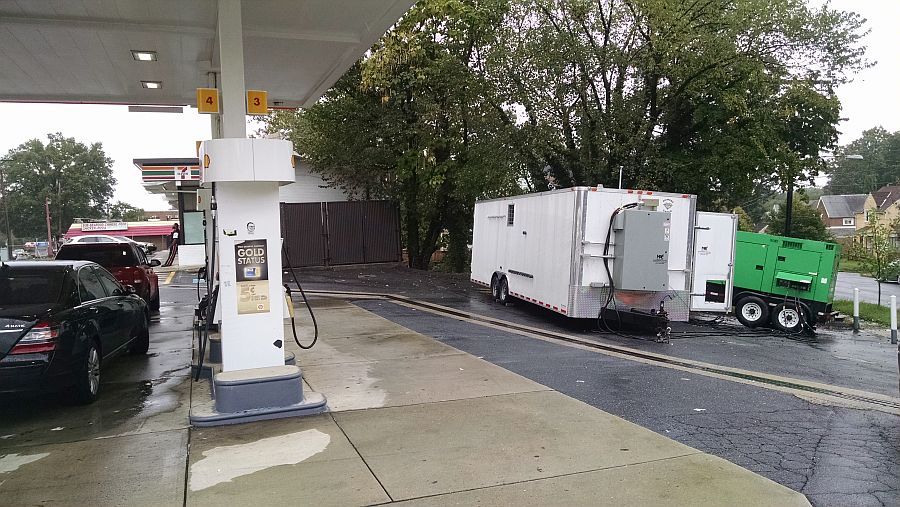
Short Term Rental System for a Groundwater Recirculation Event
MAE2 provided an existing trailer mounted system from our fleet and modified it to meet the site specific needs of the short term event. MAE2 fabricated a custom reinjection manifold to make it easy to control the flow into the injection wells. The system components were completely tested before shipping to make certain the system was ready to run on site with no downtime.
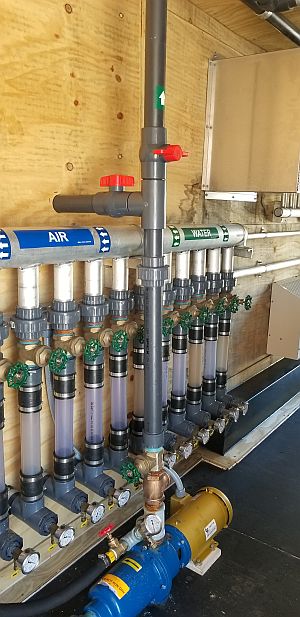
The system is a Pump and Treat and Groundwater Treatment system designed for up to 30 GPM water flow. MAE2 provided 2 QED AP4+ Pneumatic Groundwater Pumps complete with downwell air, water discharge and exhaust hoses and well caps.
The system had a Reciprocating Air Compressor connected to an air supply manifold that included pressure and flow controls. Air hose was used to connect the trailer air supply manifold with the downwell pneumatic pumps. The water discharge from the pumps connected to the multi point extraction manifold. The manifold piped the extracted groundwater to an Oil Water Separator to remove any free product gasoline. Any free fuel that is collected gravity drains into a product holding tank. A centrifugal transfer pump sends the water to a Poly Stackable Tray Air Stripper. The Air Stripper removes any dissolved phase gasoline from the water. The water is then pumped through a bag filters in parallel and two high pressure steel carbon vessels for final treatment before discharge.
The pump control allows control of the pressure and flow and the custom fabricated injection manifold allows the user to fine tune the injection volume for each well. The system is controlled by a custom PLC control panel that allows for remote access and control using web-based telemetry.
This Environmental Remediation System uses the following components and subsystems
Reciprocating Air Compressor
Rental System for a Truck Stop Environmental Remediation Project
MAE2 installed a rental Dual Phase Extraction and Groundwater Treatment system to deal with a storage tank leak.
MAE2 recently started up a rental system at an active Interstate Truck Stop facility that had experienced an underground storage tank leak in the past. The consultant had performed a pilot study at the site and developed the required system performance needed to clean the site. Costs for purchasing a new custom built system were compared to buying a refurbished system and to rental of the refurbished system. The flexibility of renting an existing system that fit the site needs was determined to be the best option.
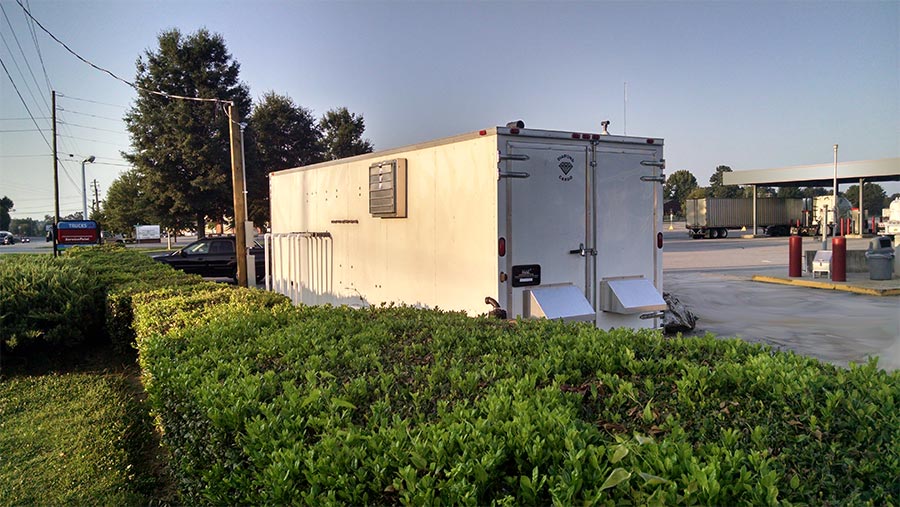
Truck Stop Environmental Remediation Project
MAE2 took an existing system from our fleet and made minor modifications. A traditional Oil Water Separator and Air stripper was replaced with an Oil Water Separator/Air Stripper Combo unit. The system components were completely tested to make the system site ready.
The system is a Dual Phase Extraction and Groundwater Treatment system designed for 10 GPM water flow and 500 ACFM vapor flow at 22” HG. There is a 5-point extraction manifold that pulls both water and vapor from the extraction wells using two 10 HP rotary claw vacuum pumps in parallel.
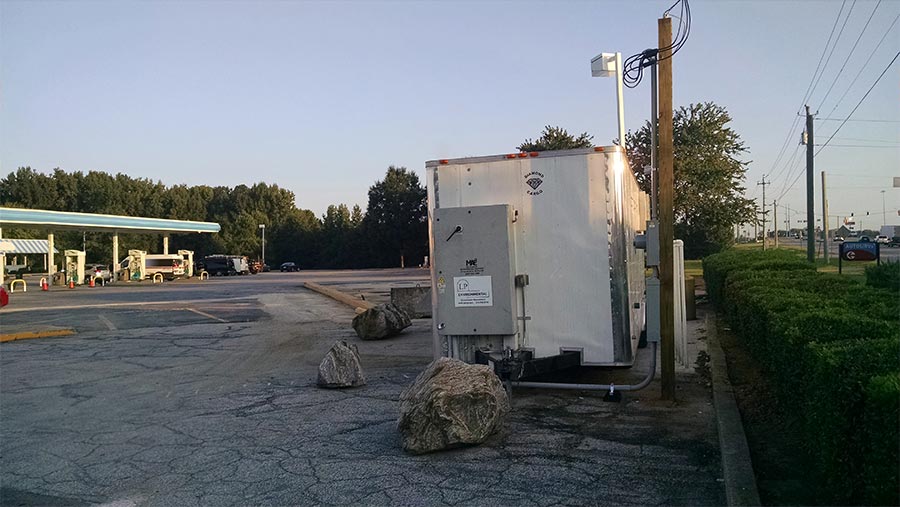
Rental Environmental System for a Truck Stop
The extracted groundwater is collected in the 120 G Vapor/Liquid separator and then pumped to an Oil Water Separator/Air Stripper combo unit using a progressive cavity transfer pump. Any free fuel that is extracted is collected in the OWS and gravity drains into a product holding tank. The water gravity flows into the Air Stripper chamber. The combo unit saves the need for an additional transfer pump and takes up less floor space. The water is then pumped through a bag filters in parallel and two high pressure fiberglass carbon vessels for final treatment before discharge. The OWS/Air Stripper pump is a centrifugal transfer pump. The system is controlled by a custom PLC control panel that allows for remote access and control using web-based telemetry.
This Environmental Remediation System uses the following components and subsystems
Multi Phase Extraction at a Bulk Fuel Terminal
MAE2 was asked to provide a bid for an environmental remediation project to clean up the groundwater and soil at a Bulk Fuel terminal for a Major Oil Bulk Fuel facility.
MAE2 was selected after a thorough review determined that the equipment and pricing proposal, for a Multi Phase Extraction system represented the most responsive and cost effective solution for the site.
The site clean-up goals required draw-down of the site groundwater followed with high vacuum Soil Vapor Extraction to clean the soils in the vadose zone and dewatered saturated soils. The water is to be treated to meet standards for surface water discharge. The contaminated vapors are to be treated using an electric oxidizer.
The Multi Phase Extraction system design is for the equipment to be contained in two enclosed cargo trailers. The use of two trailers allows for flexibility to locate and move the system around the site as needed.
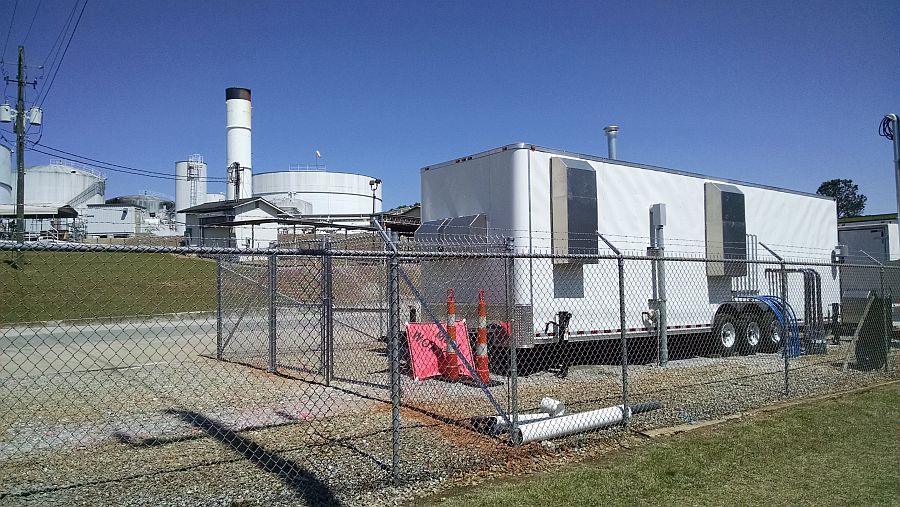
Trailer 1 Multi-Phase extraction system
Trailer 1 is a two room trailer that contains the main system control panel and a rotary screw compressor in an air conditioned non hazardous room. The air compressor provides the air supply required to operate eight downwell pneumatic pumps. Room 2 includes the air supply manifold for the pneumatic pumps and the extraction manifold SVE wells. Two 15 HP rotary claw vacuum pumps provide up to 730 ACFM at 25” HG. Any moisture and groundwater extracted is collected in the Vapor liquid separator and is then pumped over to the groundwater treatment system housed inside trailer 2 using a progressive cavity transfer pump. The extracted vapors are treated with a 600 SCFM electric oxidizer located within room 2. The oxidizer uses an automated vapor control valve to automatically adjust the vacuum to keep the vapor concentrations within the treatment range for complete destruction. Room 2 is designed to meet Class 1 Div 2 standards for hazardous locations and also includes a high LEL alarm that shuts the system down if explosive vapors are present.
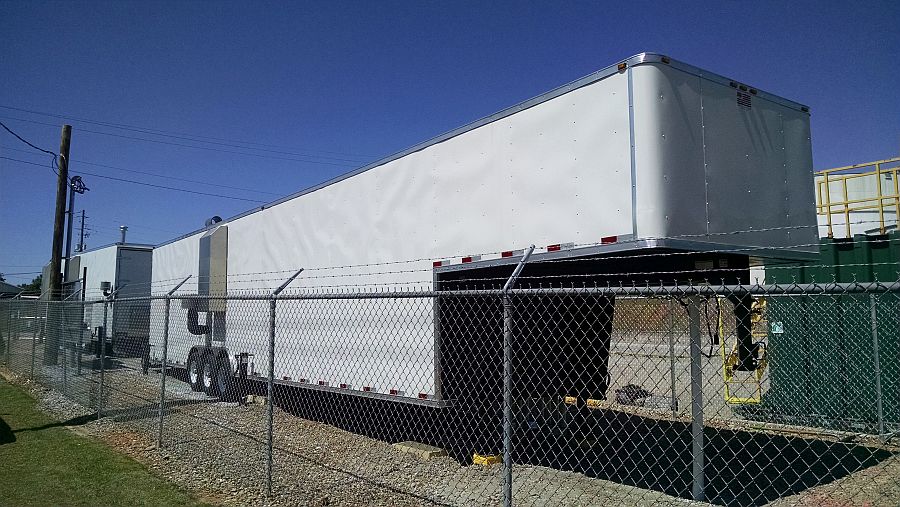
Trailer 2 Multi-Phase extraction system
Trailer 2 contains the groundwater treatment system designed treat water at flows up to 60 GPM. The trailer 2 interior is built to Class 1 Div 2 standards for hazardous locations. There is a groundwater influent manifold that allows individual well control and has a flow transmitter for each leg that records gpm flow and total gallons on the PLC control panel display. An explosion proof chemical metering pump injects into the manifold header discharge to treat the water to prevent iron scaling. The groundwater flows into a cone bottom separator tank to collect any solids and allow any free gasoline to separate to the top. Water then flows into a large EQ tank and is pumped through bag filters to remove sediment to a removable tray air stripper using a centrifugal transfer pump. From the air stripper the water is pumped through two 750 LB steel carbon vessels and then to discharge. The trailer is designed with waterproof floor and a waterproof containment equal to 110% of the holding tank volume. The trailer has a floor sump alarm to shut the system down in case of a water leak and similar to trailer 1 has a high LEL alarm.
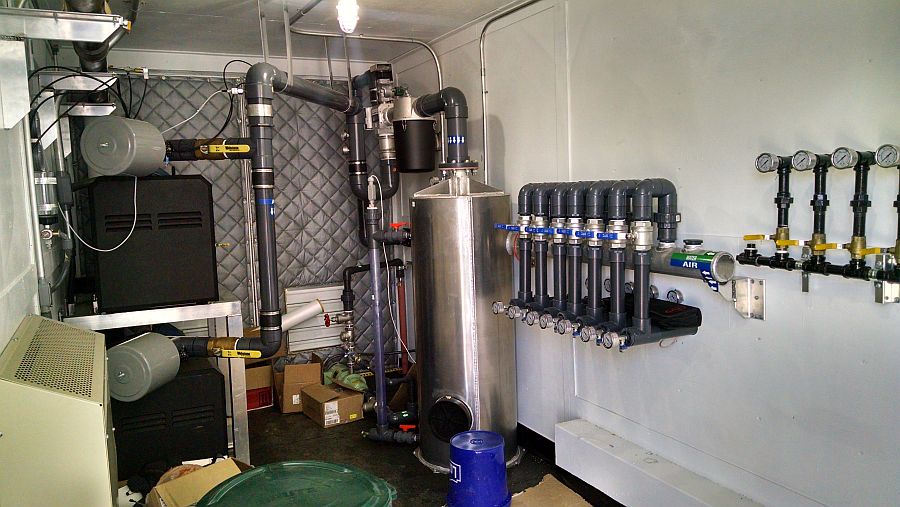
Components of the Multi-Phase extraction system
Each trailer has its own PLC control panel with a color touch screen display. The control panels are connected via an Ethernet communication cable. An operator can access either control panel from each individual panel screen or from a remote internet connection. The control panel allows each system to operate independently or to be interlocked together and records all alarms, flows, pressures and vacuum. Alarms notifications are sent via email or text and the system can be accessed remotely through a web based connection.
This Environmental Remediation System uses the following components and subsystems
Progressive Cavity Transfer Pump
Chemical metering pump