Industrial Process/Wastewater
Rail Yard Iron and Suspended Solids Treatment System Upgrade and Expansion
MAE2 was selected to provide a system to remove iron and suspended solids and to fully integrate into the operation of an existing system and controls.
While many companies have the ability to build a new system based upon a written specification, expanding an existing system and seamlessly integrating the new components and controls requires extensive industry knowledge and experience. MAE2 was selected to provide a system to remove iron suspended solids and to fully integrate into the operation of the existing system and controls.
The fouling and constant maintenance caused by the iron and suspended solids was preventing the existing water treatment system from effectively reaching the treatment goals required. MAE2’s 23 years of groundwater system design experience, our flexible manufacturing capacity and our UL control panel shop made us the perfect partner to help create a successful solution for a challenging site.
MAE2 worked with the consulting engineer to understand the existing system operation and plan the best way to augment the system and improve the treatment results. The existing system included electric and pneumatic submersible pumps that pumped fuel contaminated groundwater to an air stripper for treatment.
MAE2 worked to design and fabricate custom tanks and to design and program a custom PLC control panel to work with the existing treatment system. In the new expanded system, the extracted groundwater is pumped into a new, custom fabricated, 3000-gallon aeration tank. A chemical metering pump is used to add chemicals into the aeration tank to help precipitate dissolved iron.
Two 5 HP Rotary Claw Compressors skid mounted in parallel provide aeration in the tank at 82 CFM and 22 PSI. Fuel vapors created in the aeration tank are removed by a 3 HP regenerative vacuum blower operating at 55 CFM and 58” WC vacuum. Any residual moisture is captured in an 80-gallon Vapor Liquid Separator that includes a High-Level alarm switch and manual drain.
The vapor steam passes through the blower and then a ½ HP heat exchanger to reduce the temperature so that the 200 LB steel vapor carbon vessel can effectively remove any fuel vapors before discharging to the atmosphere. The Aeration tank is equipped with a user programmable level transmitter that controls the on/off operation of a 200 GPM, 5 HP Centrifugal Transfer Pump. The water is pumped to a custom, three stage clarifier tank.
The tank includes a polymer metering system followed by a flash chamber and electronic mixer, a flocculent chamber and electronic mixer and finally an inclined plate clarifier with hopper bottom. This removes most of the larger suspended solids and precipitated iron. The water gravity feed into a custom, 1000 gallon filtration feed tank. In order to remove any fine suspended solids, the water is pumped through a fully automated, four vessel, sand filter system.
The sand filter includes a 3000 gallon, backwash water tank and a 3000 gallon, backwash solids tank. The system PLC control panel uses pressure transmitters and automated ball valves to backwash the sand filters and pumps the captured solids to the holding tank without stopping treatment flow. A 63 GPM sludge pump controlled by a user programmable level transmitter pumps the collected solids to a custom, 3000 Gallon Settling Tank. The tank has a sludge/solids settling basin in the bottom and a custom designed liquid decanting valve system to drain liquids. The treated, solids-free water, effluent from the sand filtration system is pumped to the existing air stripper for final treatment and removal of any remaining fuel.
This Remediation System uses the following components and subsystems
Regenerative Vacuum Pump
Sand Filter
Rotary Claw Compressor
Incline Plate Clarifiers
Chemical Pre Treatment Systems
Vapor Phase Carbon
Water Treatment System at an Aeronautical Launch Center.
MAE2 was awarded a project after a competitive bid process to build a water treatment system at a former component cleaning and refurbishment workshop at an aeronautical launch center.
The site had been a parts cleaning facility that used chlorinated solvents such as Trichloroethylene (TCE) to refurbish components. The consultant’s goal is to extract contaminated groundwater from 3 wells at the end of the plume contamination area and strip the TCE from the extracted groundwater. The clean water is then re-injected into 8 injection wells to help control the groundwater flow and prevent additional growth of the contaminated plume.
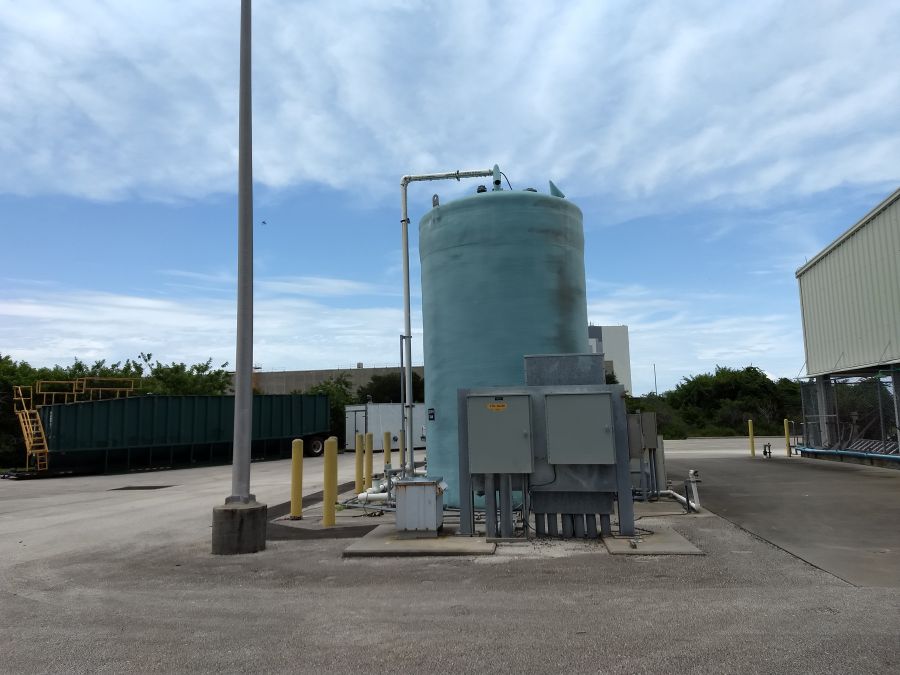
Former component cleaning and refurbishment workshop at an aeronautical launch center
The water treatment system contained a three point groundwater extraction manifold. Groundwater is pumped from three wells using electric submersible pumps. Each manifold point includes individual water flow meters to record gallons per minute from each well. The manifold header is plumed through two bag filter housings and then to a 300 gallon inlet EQ tank. The bag filters remove any suspended solids and sediment from the groundwater.
An inlet flow transmitter displays total gallons pumped and the GPM flow rate. The water is pumped by a centrifugal transfer pump from the EQ tank to a Stainless Steel removable tray air stripper. The EQ tank and air stripper both include water lever transmitters that show the current water level and allow user adjustable pump on/off and alarm set points. After the water is treated in the stripper it is pumped by another centrifugal transfer pump through two more bag filter housings to remove any remaining sediments or solids to the injection manifold.
The manifold has a groundwater flow totalizing transmitter and seven individual injection legs. Each leg has a solenoid valve for on/off and alarm control, a pressure transmitter and an individual water flow meter.
The water treatment system is built inside an 8’x20′ custom steel building with water proof secondary containment and a floor sump alarm. The building also includes air conditioning to help the equipment and controls operate in the local ambient temperature.
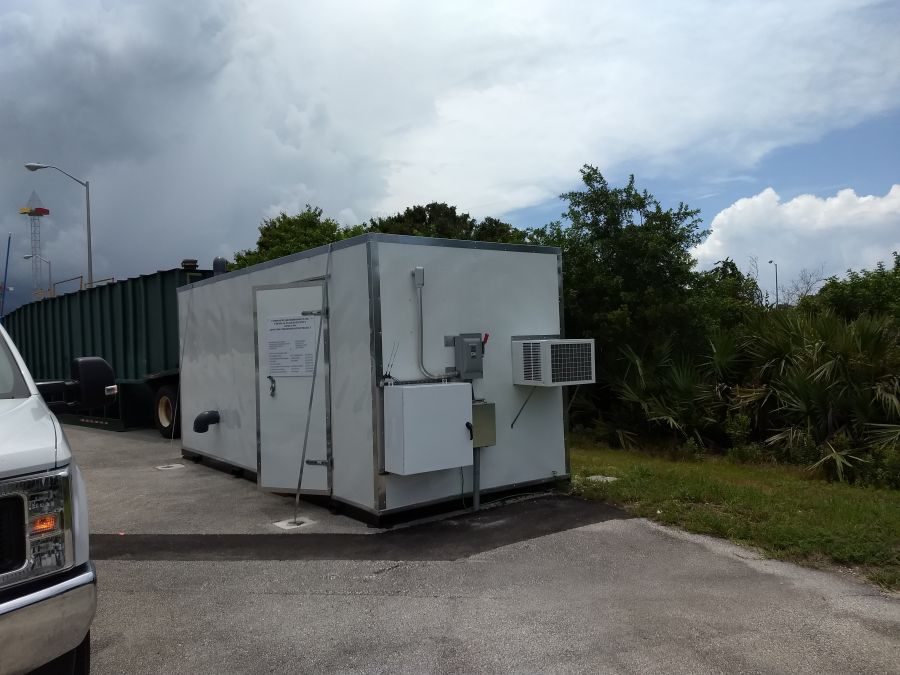
The water treatment system is built inside an 8’x20′ custom steel building
The system controls include a PLC based panel with touch screen controls and full web based cellular telemetry control and alarms. The controls allow the consultant to view and change all of the systems setting including pressure, flow, and level.
Components used in this system:
Centrifugal transfer pump
Bag filter housings
Removable tray air stripper
PLC control panel
Industrial Components for Wastewater Treatment Systems
Many of the requests MAE2 receives are for single components to improve an industrial process or help remove oils or other contaminants from a waste discharge.
Are you looking to replace an existing component or add a piece of treatment equipment to meet permit conditions or simply improve the quality of the liquid or air used in a process?
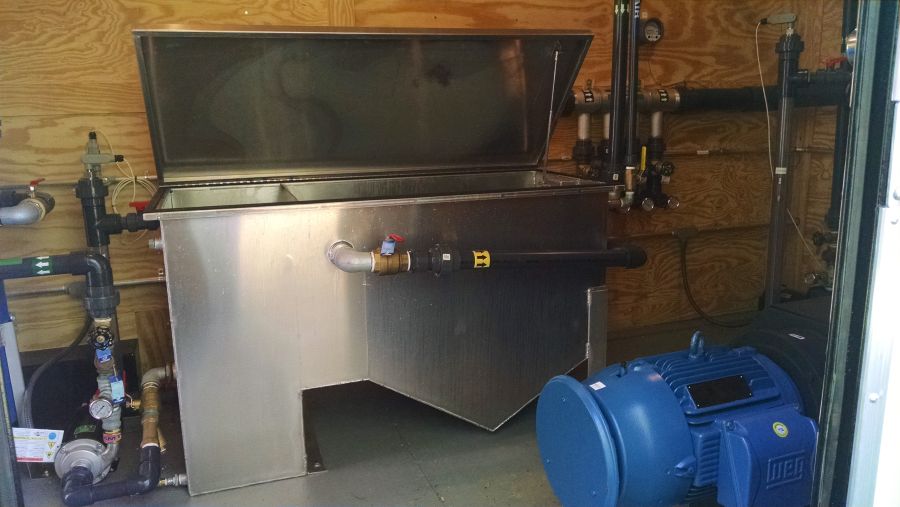
Oil water separator for industrial water treatment
If you need a Vapor Liquid Separator to remove moisture from a process air flow, an Oil Water Separator to remove free oil droplets from a process discharge, or Carbon Treatment to clean air or water discharges MAE2 has the experience and knowledge to help you find the most efficient and cost effective solution.
MAE2 can help with anything from removing oils from shop floor wash water, to creating pure water using Reverse Osmosis Filtration.
The most common requests are for Oil Water Separators and Air Water Separators (Vapor Liquid Separators), but MAE2 can provide recommendations to successfully remove particulates, suspended solids, and dissolved contaminants.
MAE2 can provide these items as standalone units or with the additional switches, controls or components needed to integrate them fully with your existing site and equipment.
Industrial Components for Wastewater Treatment Systems often use the following components and subsystems
Marine Research Groundwater Treatment System
Variable Flow Industrial Process Treatment System
MAE2 was tasked with designing a system to treat process water to remove iron and fuel contamination for a marine research center. The research center used local groundwater to supply fresh water to fish tanks used for scientific research. The groundwater had been impacted with fuel from a nearby gas station and was high in iron bacteria. The fuel needed to be removed from the water to keep the fish healthy and the iron needed to be removed to keep it from fouling the drum filters that provided the filtered water required in the tanks. The system needed to handle flows that ranged from 8 GPM to peak flows of 45 GPM. The facility wanted to reduce electrical power costs by only operating at full power during peak times and adjusting the power down during lower flow periods.
MAE2 designed a system with a fully automated PLC control panel. The PLC constantly measures the incoming flow rate and uses Variable Frequency Drives (VFDs) to adjust the motor speeds to match the flow rate. The PLC controls also monitor system pressures and automatically initiates a system backwash to clear the iron filters and reduce manual cleaning labor. The system is designed to keep a continuous water supply to the research tanks even during the back wash cycles.
This turnkey MAE2 solution reduces on site maintenance, electrical power usage, and provides treated process water in a compact fully automated package that adjusts to the constantly changing site conditions. This system is expected to go online this upcoming summer.
Click on diagram to see another.
The groundwater treatment system consisted of an aeration chamber and slant plate clarifier to precipitate and collect iron, a removable tray air stripper to remove the dissolved gasoline, a back-washing filtration media system to remove any fine particulate and finally liquid carbon media vessels as a final safety to remove any potential remaining gasoline.